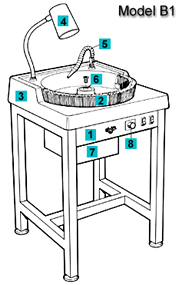
1. Base: The frame is all welded construction using 2" heavy-duty 1/8" tubular steel. Machinery grade 3" adjustable levelers. Chip-proof powdercoat enamel. Individual switches for light, motor, pump. 8' line cord
2. Splash Guard: This very unique brush stops coolant spray that comes off the disc. It need not be removed for longer pieces, as the glass passes right through the bristles without affecting their ablility to stop the spray
3. Housing: Molded polyethlene which will not rust
4. Light: Industrial 100 watt Moffatt gooseneck lamp. Easily adjusts to any position
5. Coolant: Completely plumbed for use with either a recirculating pump or city water supply. This type of flexible spout makes it easy to diret a heavy stream of coolant to any area of the grinding disc
6. Drive Assembly: An ultra-precise ground 1" stainless drive shaft and a 3 3/4" stainless mounting flange provide a drive surface which totally eliminates vibration. The grinding disc is held in place by a countersunk screw, so that the grinding surface is totaly flat. Upper and lower ball bearings are permanently sealed and lubricated industrial grade
7. Motor: Fixed-speed motor is a 1 HP "industrial" quality Baldor, or the variable-speed motor is a permanant magnet "industrial" quality Magnetek
8. Speed Control: Comes only with the variable-speed motor. An electronic control that produces a constant torque and includes current limiting to protect both the permanent-magnet motor and control. By changeing the dial, the drive shaft speed is continuously varible between zero and 1100 RPM
Variable Vs. Fixed Speed
There are two models. A fixed-speed machine which is set at 1100 RPM, or a variable speed version which is adjustable from 1100 RPM to zero by just turning a knob.
1100 RPM results in a peripheral speed (in the working area on the disc) of 4500 ft/minute, which is the perfect speed for grinding glass. This can easily be changed in the field to accommodate other types of grinding media.
If the machine is going into a production beveling shop and will be used for only a single purpose, a fixed-speed model is probably the best choice.
The variable-speed model is preferable in the following situations:
1. If it is the only grinder in the shop, it should be as versatile as possible.If a polishing pad is to be used on the disc, a slower speed is preferable for polishing.A cold-glass working shop needs the ability to slow the disc for delicate pieces.
2. A lapidary shop prefers different speeds for different materials.
The B1 is designed for heavy production use.The precision-ground, one-inch mounting shaft and flange are solid stainless steel and the 1/2"-thick housing is molded fiberglass so that rust will never be a factor.The shaft ball bearings are oversized, sealed and permanently lubricated. The motor choices are the best available. The fixed-speed motor is a Baldor, with electronic starter. The variable-speed motor is a Magnetek. Its electronic speed control has current limiting to protect the motor and control.The base is 1/8"-thick steel tubing. Every aspect of this grinder is over-designed to create a machine that will last trouble-free.
Disc Size
There are primarily two diamond disc sizes used on the B1, 20" and 16". A production shop that will be grinding a good part of the week should be using 20" discs. If the usage is one day a week or less, then a 16" disc will be adequate unless, of course, the size of the work pieces require a larger disc.
Grit Size
For the rough grinding, an 80 or 100 grit is most popular, and for the smoothing step, a 360 or 600 grit. The 80 and 360 are usually used together, or the 100 and 600. As an economical first step, purchase a single B1 and switch the roughing & smoothing discs. It takes less than 30 seconds to change discs
Flush-Mount Discs
This unique mounting arrangement results in a completely flat grinding surface. This allows use of the total grinding surface without being concerned about the work piece striking a mounting nut. It also makes it very easy to turn the disc upside down so that the new adhesive-backed grinding or polishing pads can be used on the other side.
|