Standard Diamond Wheels (pictured above)
The hole diameter is 12 and bushings are furnished for 3/4", 5/8" and 1/2" shaft size. Wheel thickness is 11/2". 60 and 1200 grit are also available. The coarse wheels (60 to 180 grit) employ a raised cross-hatched pattern, which produces an interrupted cutting surface. It is far more aggressive than a smooth pattern and because there is one-third more diamond, it lasts just as long. The fine wheels (360, 600 & 1200) are a smooth, uninterrupted surface. Any grit is available in any pattern. These wheels use nickel to bond the diamonds. When used for beveling glass, the 8" wheel can generate an inside curve as small as 11/2" radius. 6" and 4" wheels will generate a 1" and 1/2" radius respectively.
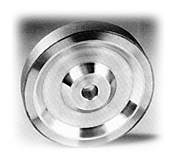
Metal Bond Diamond Wheels
This type of wheel with its 1/8"-thick band of solid diamonds is meant for high-volume production. Metal bond means that the diamonds are embedded in a sintered metal matrix. This type of wheel has a very long life. It will last 6 to 10 times longer than a standard diamond wheel and cost only two to three times as much. A metal bond wheel is best suited for rough grinding and is the same price irrespective of the grit size. The standard hole size is 1" and bushings for 3/4", 5/8" and 1/2" are furnished. The 10" diameter wheel can be used on the Glastar B7 upright. The entire face of a metal bond must be used evenly to avoid grooves. However, Glastar can reface the wheel if this happens.
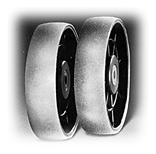
Radius Wheels
This wheel can grind a "radiused" concave depression in the work piece. It permits high visibility at the point of contact with the work piece allowing precise control of the cutting outline. A radius wheel is very popular with the hot glass artist for removing punty marks. These wheels use nickel to bond the diamonds. The hole diameter is 1" and bushings are furnished for 3/4", 5/8" and 1/2" shaft sizes. Wheel thickness for the 4" wheel is 1" and 11/2" for the 6" and 8".
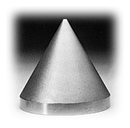
Cones
This type of wheel is used by cold glass workers and bevelers to obtain very small, tight inside curves. They are difficult to use. Beginning bevelers should use standard flat face wheels and graduate to cones later. They are easier to use on a horizontal, rather than a vertical shaft. The minimum shaft speed should be 3600 RPM. However; faster would be better. They are 60 degree cones and are 3 in diameter. The standard mounting hole is 1"-14 RH, but any thread size can be ordered. These cones use nickel to bond the diamonds and only a smooth pattern is available. Any grit can be ordered.
Don't Waste Diamonds
When converting from a stone to diamonds, be certain that the drive shaft is running at the proper speed. The optimum speed for grinding glass, and most materials, with diamonds is about 4500 ft/min. This can be varied by as much as 30% in either direction and still obtain satisfactory results. The table shows the ideal RPM for various wheels. Be certain there is a plentiful supply of coolant playing on the diamond. This insures maximum life.
Wheel Diameter |
4" |
6" |
8" |
10" |
Recomended RPM |
4000 |
3000 |
2000 |
1750 |
Most grinding operations are composed of two steps. The first is rough grinding, which removes most of the material and shapes the piece. This is achieved with a coarse wheel (60 to 180 grit). Fine grinding is the second step (360, 600 or 1200 grit) and leaves a smooth matte finish in preparation for the polishing steps. For glass grinding, by far, the most popular combination is 100 grit for roughing and 600 grit for smoothing. |